Mazda Still Makes The 13B Rotary Engine To This Day
Visit the backstage of the continuous production of the 13B rotary engine.
This story was translated and adapted from Classic Mazda. Find the original version here.
The dream engine doesn’t end with a dream. People, factories, and aspirations support its continued production.
One day in 2021, Hiroshima. At 8:30 in the morning, the dimly lit factory lights turned on, and soon machinery as far as the eye can see begin to growl low.
This is the Mazda 2nd Powertrain Manufacturing Department – a factory that manufactures rotary engine and 13B type parts. Yes, the rotary engine isn’t done yet.

Back when Mazda was still called Toyo Kogyo, they had a grand dream for the future of sporty automobiles. Mazda believed in the smooth and vigorous character of the rotary engine and committed to its success.
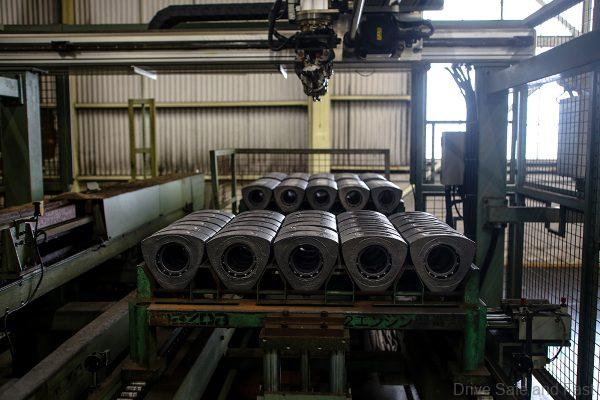
Here’s a tour of the factory that made that dream come true for decades and is still running today to produce new engines and parts for enthusiasts around the world.

The same machines and process
Even in 2021, the 13B rotary engine is painstakingly manufactured one by one. The same equipment and processes are used by a small group of experts to make these engines.
Tetsuya Sato is a veteran team member who has been involved in rotary engine making for 36 years.
“Manufacturing of rotary engine parts at this factory began in 1973. Since the equipment such as machine tools are also from the same period, we have been working for nearly half a century… Since the accuracy of the machines is absolutely essential, daily maintenance is indispensable. Many people don’t know, but Mazda continues to manufacture rotary engines.
We stopped installing it in new cars after production of the RX-8 ended in 2012, but engines were still being made after that. We continue to manufacture 13B replacement parts and the bare engine body assembled with new parts. That is why this factory remains operational,” Mr Sato said.

“These machines old machines are not as dexterous as today’s computer-controlled machines. All of the machines here are cutting machines. Since the blade can only be moved in one direction, it is necessary to set it on the next machine and perform the next processing after finishing one process.
“It’s an old-fashioned piece of equipment, but it’s a wonderful thing that makes you feel the essence of our forebears’ commitment and ingenuity.”
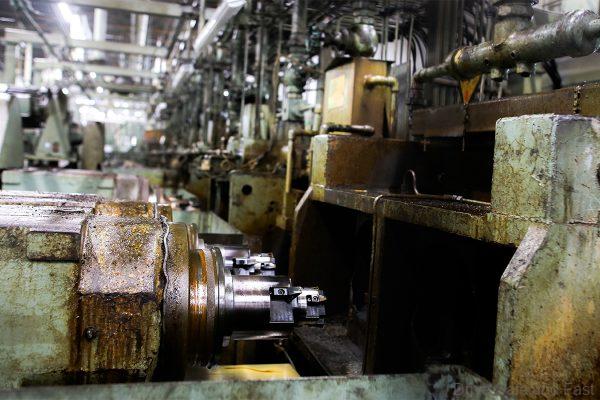
Mr. Sato shows the production process of the 13B.
Maintaining the best production environment is the first step for the highest quality
“Here, we will make a groove to create a part called an apex seal. The apex seal that is assembled to the three vertices of the triangular rotor is an extremely important part for the rotary engine to perform at its best. “

Yoshikazu Washio, another team member explains.
“The design value of the groove width is 2 mm. It is finished with an accuracy of -5 microns and plus 12 microns (1 micron = 1/1000 mm). This is done by carefully and slowly scraping with a rotating whetstone. This work begins with carefully checking the thickness and condition of the grindstone before starting processing. The grindstone gradually becomes thinner over time.
Also, the surface of the grindstone gets worn or uneven. If it is, the inner wall of the groove will also be similarly imperfect. Of course, if there is even a slight malfunction in the machine, it will ruin the rotor that has gone through many steps so far. So, it’s very important to keep making sure that you are in the best working environment every time.”

Mr. Washio is also a major veteran, having spent the last 35 years building rotary engines here.
“There are a total of seven people involved in the rotary engine manufacturing site at this factory. We do the first half of the rotor housing processing in another factory building on the same site. There are only 10 people in total.
That number of people manufactures not only the rotor, but also the rotor housing, side housing, eccentric shaft, and all the other parts needed for a rotary engine. I think there is a strong sense of companionship here.” said Mr. Sato with a laugh.
13B type, a team of only 10 people who completely separate all 10 variations
Under this system, which Mr. Sato introduced with a smile, an average of 200 to 400 rotary engine parts are shipped to the world every month from this factory.

Hiromichi Abe and Naoki Mizutsu, who are both foremen comment:
“The 13B rotary engine actually has as many as 10 variations, depending on the model and specifications of the vehicle. The finish of the parts used in each is different. These parts can be ordered from us wherever you are in the world.
Depending on the part, it may take 1 to 2 months to complete all the processing processes. It may be necessary to combine multiple completed parts into a single unit.
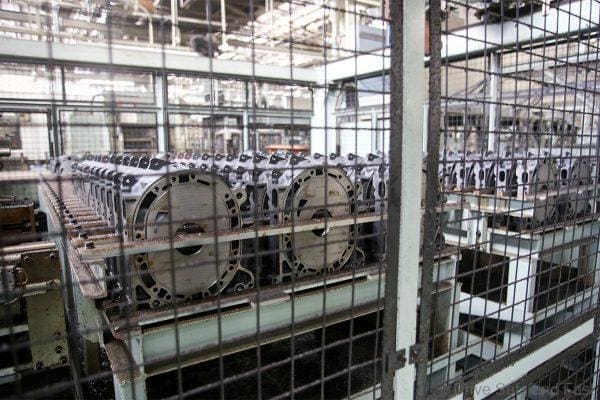
Everyone who works here has the experience and skills to do multiple tasks perfectly. It’s normal to see the person who was in front of one machine doing work in front of another machine that requires different skills. This is not the kind of production that can happen if everyone just does one thing only.”

When asked what kept them motivated to continue their difficult work, Mr Sato answered:
“Everyone who entered Mazda in the same generation as me longed to build rotary engines. Although it is not installed in new cars now, I can understand why it is held in such high regard still. And I know that there are many customers all over the world who bought Mazda cars equipped with rotary engines, so the work we put in is justified.
It is an engine that requires meticulous work, but having a team where everyone shares equal responsibility is the greatest joy of working at this factory. “