Paint Booths In Daihatsu’s Kyoto Plant Use 44% Less Energy Thanks To Redesign
Daihatsu has innovated to reduce energy consumption in one area of production.
While it’s important to reduce local emissions from exhaust fumes, the biggest impact to the environment usually comes from the production side of things. That’s why many car companies are putting more more into making their production lines more energy efficient and carbon neutral. One such company is Daihatsu – the long-time technology partner of Perodua.

Back in September 2018, Daihatsu began to upgrade its car production plant in Kyoto. The Oyamazaki Plant had been in operation since 1973 and it was discovered that 65% of the plant’s overall energy consumption went into the automotive painting process. With that in mind, Daihatsu got to work and the results were:
- 15% reduction in the number of processes
- 30% reduction in time to produce one vehicle
- 42% reduction in CO2 emissions

They did all this by increasing the use of Set Parts Supply Systems (allowing multiple people to work on one vehicle), implementing tranverse feeding of vehicles to shorten process lengths, installing air conditioning recycling in dry booths, and investing in solar energy for the plant. Daihatsu also introduced an ultra-high transfer efficiency coating machine and also fully automated the coating process for a more compact paint booth too.

Overall, this has resulted in a 44% reduction in energy consumption in the paint booth section of the plant compared conventional paint booths. Although the changes were relatively minor, in the grand scheme of things they were important. As such, the Daihatsu has been presented the Energy Conservation Grand Prize Award by the Energy Conservation Centre of Japan (ECCJ). The award ceremony will take place on the 1st of February 2023.

Daihatsu has stated its intention to realise carbon neutrality at its plants by 2035. The company also stated that it would deploy the technology and know-how from this project to other domestic plants and to those overseas. We wonder if these changes have already been implemented at the Perodua plant in Rawang.
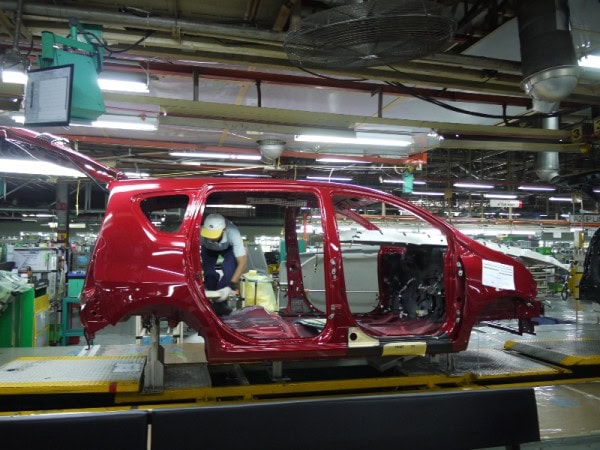