Nissan Has Revolutionised Carbon Fibre Part Production
Electrified cars are pretty efficient, especially when compared to vehicles with traditional internal combustion engines. Typical petrol-powered cars only utilise about 30% of the energy stored in the fuel to move. The rest of the energy is wasted in the form of heat, noise, vibrations and exhaust fumes.

However, electric vehicles, even mild hybrids have one major disadvantage versus petrol or diesel powered cars: weight. Batteries are heavy. Even plug-in hybrid vehicles are super heavy. The Volvo XC90 T8 Twin Engine, for instance is about 325kg heavier than the T5 petrol model. The BMW X5 xDrive45e is 375kg heavier than the the xDrive40i.
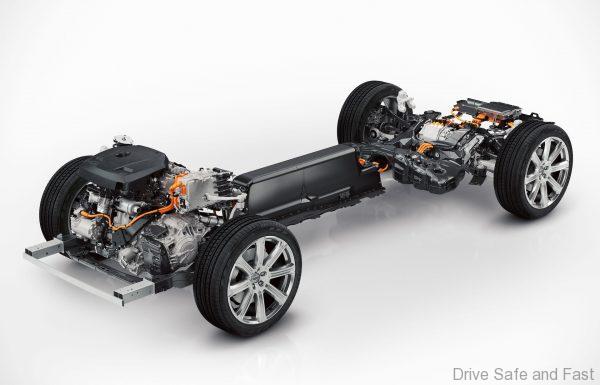
With that in mind, Nissan are looking for ways to make cars lighter as electrification becomes the norm. To this end, they’ve come up with a new process that cuts the production time for carbon fibre reinforced plastics (CFRP) by half.

CFRP is extremely strong and extremely light. They’re ideally suited to replace steel in vehicle bodies, but they take a long time to develop and a long time to produce. That in turn affects how much it produce, as metals can be more easily shaped and stamped.
With this new CFRP production method, Nissan can start to include the material in more mass-market electric vehicles. We wouldn’t be surprised if future electric and electrified vehicles by Nissan will be lighter than their competitors’ thanks to this technological leap forward.

They held a press conference to announce this revolution, which you can watch here:
Here’s another short video they produced that gets straight to the point.
A material used in airplanes, rockets and sports cars may find its way into more mass-market cars thanks to a new production process developed by Nissan.
The new process speeds up the development of car parts made from carbon fiber reinforced plastics, or CFRP. Lightweight yet extremely strong, the material can be used to make cars that are safer and more fuel efficient. It can also lower a car’s center of gravity when applied to upper body parts, making it more agile and exciting to drive.
Nissan aims to use the new process to mass-produce CFRP parts and introduce them in more cars for customers. The innovation can cut the lead time to develop such components by as much as half, and cycle time for molding by about 80%, compared with conventional methods.
While the benefits of carbon fiber have long been known, it’s expensive compared with other materials such as steel. Along with the difficulty in shaping CFRP parts, this has hampered the mass production of automotive components made from the material.
Nissan found a new approach to the existing production method known as compression resin transfer molding. The existing method involves forming carbon fiber into the right shape and setting it in a die with a slight gap between the upper die and the carbon fibers. Resin is then injected into the fiber and left to harden.
Nissan’s engineers developed techniques to accurately simulate the permeability of the resin in carbon fiber, while visualizing resin flow behavior in a die using an in-die temperature sensor and a transparent die. The result of the successful simulation was a high-quality component with shorter development time.